Form 8-K MUELLER INDUSTRIES INC For: Mar 24
UNITED STATES
SECURITIES AND EXCHANGE COMMISSION
Washington, D.C. 20549
FORM 8-K
CURRENT REPORT
Pursuant to Section 13 or 15(d) of the Securities Exchange Act of 1934
Date of Report (Date of earliest event reported)
|
March 24, 2016
|
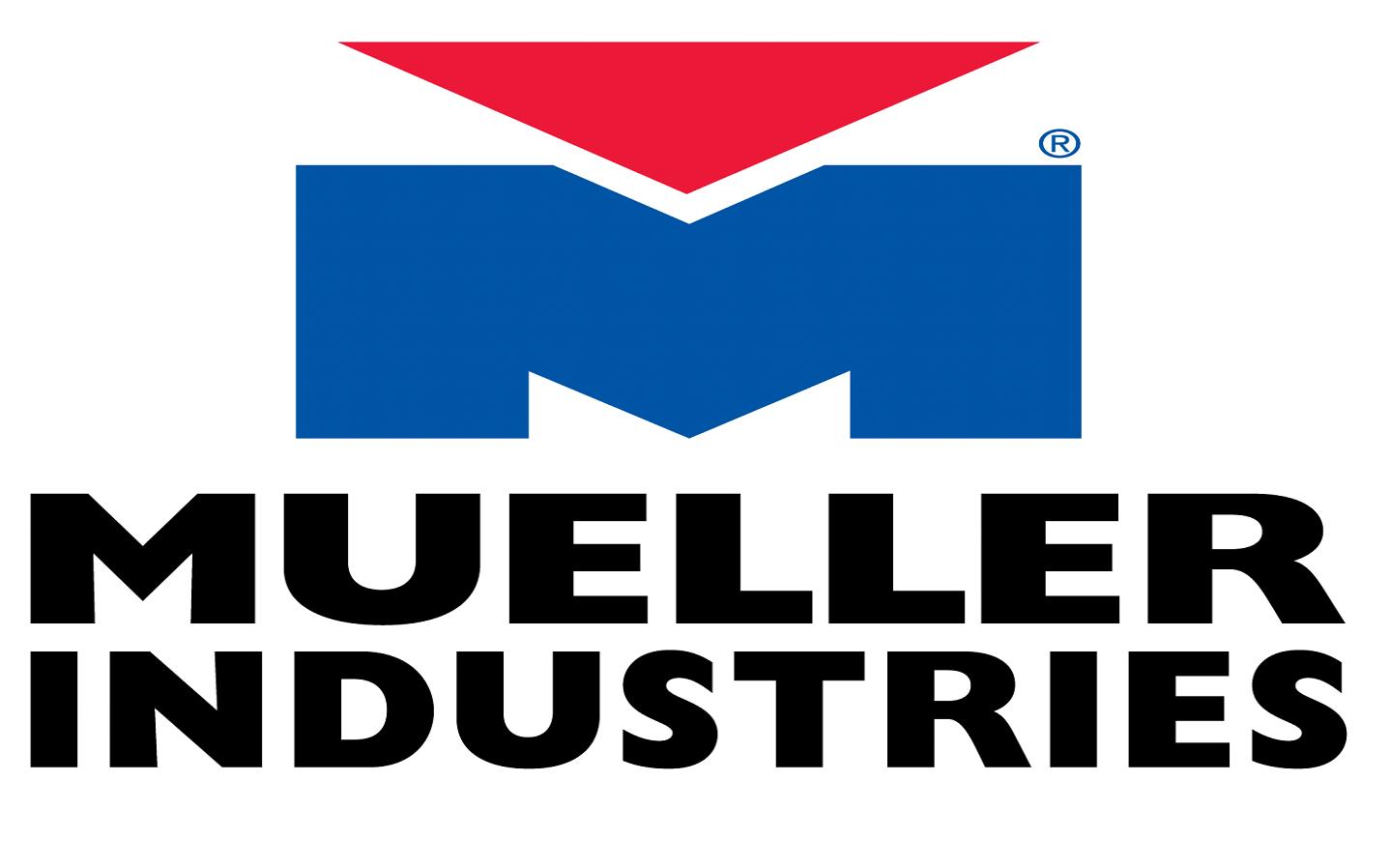
MUELLER INDUSTRIES, INC.
(Exact name of registrant as specified in its charter)
Delaware
|
1-6770
|
25-0790410
|
(State or other jurisdiction of
incorporation or organization)
|
(Commission
File Number)
|
(I.R.S. Employer
Identification No.)
|
8285 Tournament Drive, Suite 150
|
|
Memphis, Tennessee
|
38125
|
(Address of principal executive offices)
|
(Zip Code)
|
Registrant's telephone number, including area code: (901) 753-3200
Registrant's Former Name or Address, if changed since last report: N/A
Check the appropriate box below if the Form 8-K filing is intended to simultaneously satisfy the filing obligation of the registrant under any of the following provisions (see General Instruction A.2. below):
☐
|
Written communications pursuant to Rule 425 under the Securities Act (17 CFR 230.425)
|
|
|
☐
|
Soliciting material pursuant to Rule 14a-12 under the Exchange Act (17 CFR 240.14a-12)
|
|
|
☐
|
Pre-commencement communications pursuant to Rule 14d-2(b) under the Exchange Act (17 CFR 240.14d-2(b))
|
|
|
☐
|
Pre-commencement communications pursuant to Rule 13e-4(c) under the Exchange Act (17 CFR 240.13e-4(c))
|
ITEM 7.01
|
Regulation FD Disclosure.
|
On March 24, 2016, Mueller Industries, Inc. (the "Company") mailed a letter to its shareholders, a copy of which is attached as Exhibit 99.1.
Mueller Industries, Inc. does not intend for this Item 7.01 or Exhibit 99.1 to be treated as "filed" for purposes of the Securities Exchange Act of 1934, as amended (the "Exchange Act"), or incorporated by reference into its filings under the Securities Act of 1933, as amended.
ITEM 9.01
|
Financial Statements and Exhibits.
|
(d) Exhibits
99.1 Letter to Shareholders
2
SIGNATURE
Pursuant to the requirements of the Securities Exchange Act of 1934, as amended, the registrant has duly caused this report to be signed on its behalf by the undersigned hereunto duly authorized.
|
MUELLER INDUSTRIES, INC.
|
|
|
|
|
|
By:
|
/s/ Jeffrey A. Martin
|
|
Name:
|
Jeffrey A. Martin
|
|
Title:
|
Chief Financial Officer and Treasurer
|
|
|
|
Date: March 24, 2016
|
|
|
3
EXHIBIT INDEX
Exhibits
|
Description
|
|
|
|
|
|
|
|
|
99.1
|
|
Letter to Shareholders
|
|
|
|
|
|
|
|
Mueller Industries' net sales for 2015 totaled $2.1 billion, compared with $2.4 billion for 2014. Net income was $87.9 million versus $101.6 million for the prior year.
Business Overview
The housing and commercial construction industries enjoyed continued growth in 2015. New home construction continued its multi-year upward trend with housing starts rising 10.7% over 2014. Spending in the commercial construction segment was also up a healthy 9% over 2014, growing for the second consecutive year. All of this was positive for Mueller Industries' Piping Systems Group, which is largely dependent on the building construction sectors. The Piping Systems Group comprises approximately 68% of the Company's revenues.
Positive news in the building construction industry was offset by the contraction in demand in the industrial-related markets, which both our Industrial Metals and our Climate Products Business Groups serve. Combined, these two business groups make up the other 32% of our Company's revenues, and both experienced associated declines. Driven in large part by OEMs, the softening in these markets prompted customers to reduce inventories and to in-source products to help maintain employment levels. In addition, the strengthening of the US dollar invited increased import competition and with that, a few more challenges.
As a result, the Company's overall unit volume ended the year on par with 2014. In addition to the contraction in the industrial sectors, we did not benefit proportionately from the positive building construction environment in 2015. During peak periods of demand, our supply was constrained in our US copper tube business as we were in a critical phase of the Copper Tube modernization project, which temporarily hindered production. This is discussed in greater detail below.
We note that the single most discernable impact on our results in 2015 was the worldwide freefall of copper prices, which declined 20% from levels experienced in 2014. Copper is the principal material used in the majority of our product offerings across all business segments. Consequently, copper's price decline largely contributed to a 13.4% decline in reported revenues, and had an adverse effect of more than $25 million on our operating income.
Operations Overview
Our Company made significant operational improvements in 2015, fueled by $201 million worth of investments in capital expenditures and acquisitions throughout the year. Our most prominent spending for capex was in our Brass Rod and Copper Tube mills, where we are committed to reinvest in our core businesses to be the low-cost producer.
The culmination of a four-year effort, the modernization of our Port Huron, Michigan Brass Rod mill was completed in 2015. The equipment is fully commissioned and operating as expected as of the latter part of the fourth quarter. With this new, faster, more capable and reliable technology, we hope to achieve world-class levels of quality and competitiveness.
Over the same time period, our Copper Tube plant located in Fulton, Mississippi also has been undergoing a modernization effort. The Fulton project is considerably more extensive and costly. In 2015, we successfully installed the bulk of the extrusion and drawing equipment, while we continued to operate our mill with manageable disruption. We remain on track and anticipate completion of the Fulton modernization in 2017.
Projects such as these, from concept to completion, are quite expansive and complex. Long lead times for building the equipment, extensive effort for preparing our facilities and coordinating installation, as well as the commissioning of the equipment and training of our team members extend these projects over multiple years. Our investments prepare these businesses well for the future.
We are committed to investing in areas that extend our core and build new competencies and capabilities for future growth. In that spirit of commitment, we were pleased to complete the new Mueller Lineset manufacturing plant in Fulton, Mississippi. Completed in November 2015, this new plant is optimally located adjacent to our Fulton Copper Tube mill, which provides the feedstock for lineset production. The new plant will increase capacity, reduce manufacturing and supply chain costs, and allow us to expand our product range, including the manufacture and distribution of our new polyethylene linesets.
We also completed the building expansion at our Westermeyer Industries business in Bluffs, Illinois. Westermeyer manufactures vessels that support the air-conditioning and refrigeration systems. The extension of the facility enhances our capability to manufacture more and much larger vessels. In addition to supporting the increasing demand of customers we currently serve, this investment enables us to grow into new markets such as industrial refrigeration, chemicals, and the oil and gas industries.
Our investments extended across the Atlantic to Europe, where we completed the consolidation of the Yorkshire Copper Tube mill in Kirkby, UK into our Wednesbury Copper Tube mill in Bilston, UK. Our Bilston operation is one of the most modern of its kind in Europe, and all of the necessary improvements are complete and operational. We closed the Kirkby operations in August of 2015, and all redundancy and related expenses were accounted for and recorded by year-end.
In addition to these capex projects, our ongoing focus and investment in product development yielded the commercialization of our new trans-critical CO2 (XHP) copper piping system. Our new XHP product was developed to support the increasing demand for systems requiring extra high pressures and temperatures. Mueller Industries has long been a trusted leader in refrigeration systems. XHP expands our offerings to meet new regulatory requirements related to promoting greener, more efficient systems. XHP is a complete system which includes pipe, valves, and fittings.
The above investments consumed a large percentage of the $29 million we recorded in capital project spending in 2015. A more extensive amount of our cash was deployed in our landmark year for acquisitions. The completion of four acquisitions during 2015 used a total of $172 million of cash on hand.
In March of 2015, we completed the acquisition of Turbotec Products. Located in Hickory, North Carolina, Turbotec specializes in high performance heat exchange technologies, with approximately $22 million in annual net sales. This acquisition complements our Climate Products Business Group and expands the product offerings and customer base of our current shell and tube heat exchange business.
At the end of June, our second acquisition was completed with the purchase of Sherwood Valve Co. Sherwood has operations in Washington, Pennsylvania and Cleveland, Ohio with net sales of $45 million. In addition to the Sherwood line of compressed gas valves, Sherwood is the parent to the Superior refrigeration valve brand. The Superior line of refrigeration valves complements Mueller Streamline's own extensive history in refrigeration products, including Streamline valves, driers, fittings, and other related products. The Sherwood acquisition also carries with it strong competencies and capabilities in the areas of brass manufacturing, forging, and machining. These will complement Mueller Industries' brass forgings and machining businesses, and will support our strategic growth plan in our brass value-added products platform.
Our third acquisition, Great Lakes Copper, was completed in July. Great Lakes Copper is located in London, Ontario, and had net sales just shy of $300 million US in the 12 months prior to our acquisition. Great Lakes Copper is the sole manufacturer of copper tube and linesets in Canada. This acquisition not only expands our manufacturing footprint geographically, but also broadens our capabilities in the US with the unique products and process competencies that Great Lakes Copper possesses.
Our final and largest acquisition was completed in September. Early in 2015, Mueller Industries joined forces with Atlas Holdings LLC, out of Greenwich, CT, to acquire Tecumseh Products Company (formerly Nasdaq TECU). Tecumseh is a recognized leader in the manufacture of hermetically-sealed compressors that service the refrigeration and HVAC markets globally. Operating in 8 countries with over 5,000 employees, Tecumseh's net annual sales exceed $600 million. We completed the transaction on September 22, 2015.
Our partnership with Atlas leverages Mueller Industries' operational and commercial strengths in the air-conditioning and refrigeration sector with Atlas' proven excellence in rehabilitating companies with diverse complexities and challenges like those faced by Tecumseh. In the short period of time since our acquisition, our optimism about Tecumseh's potential continues to increase, despite the long road ahead.
Outlook for 2016
Here in the US, despite consecutive years of improvement, housing starts remain at relatively low levels by historical standards. With 30-year mortgage rates below 4%, unemployment at 8-year lows, and the supply of homes for sale at historically low levels, the housing industry has ample potential to improve. The commercial construction industry is also coming off consecutive years of improvement driven largely by private sector spending. Eventual investment in US infrastructure, schools, and other public institutions would encourage our expectation for continued improvement in the commercial construction industry, albeit at more modest levels than we saw in 2015.
Globally, things have become clear as mud. Commodity deflation, currency weakness abroad, and the potential of Brexit are all symptoms of broader economic uncertainty. The outlook for copper is centrally important to Mueller Industries' business. We believe that the significant impact to our FIFO businesses in 2015, due to the decline in copper, is not likely to repeat itself. Copper ended the year at LME $4,702 per metric tonne ($2.13 per lb). Copper prices near $2.00 per lb are at or below the cash costs of production of some mining properties, which may ultimately result in constrained supply.
As we navigate into 2016, we feel confident about our company as we head into our 99th year of business. In 2015 our Company generated $160 million in cash from operations. Net of the $201 million in investments we made, we ended the year with $275 million in cash on hand. This combined with a low level of debt gives us a rock-solid balance sheet and the powder to continue to fund opportunities that we feel will support our growth strategies and make us a better, stronger company for the future.
In Closing
In essence, our 2015 financial results belie the significant body of work completed this year. Our investments contributed key puzzle pieces in positioning our Company for the future. All of the businesses within our 3 business groups – Piping Systems, Industrial Metals, and Climate Products – are well capitalized, excellently led, and have very clear and focused roadmaps for 2016 and beyond. We welcome the vast number of newcomers to our Company this past year. In conjunction with the talented and dedicated team of Mueller Industries employees, they will continue the tradition of making Mueller Industries the best of the best. We appreciate the dedication of all our employees and we are proud of their many accomplishments this past year.
Sincerely,
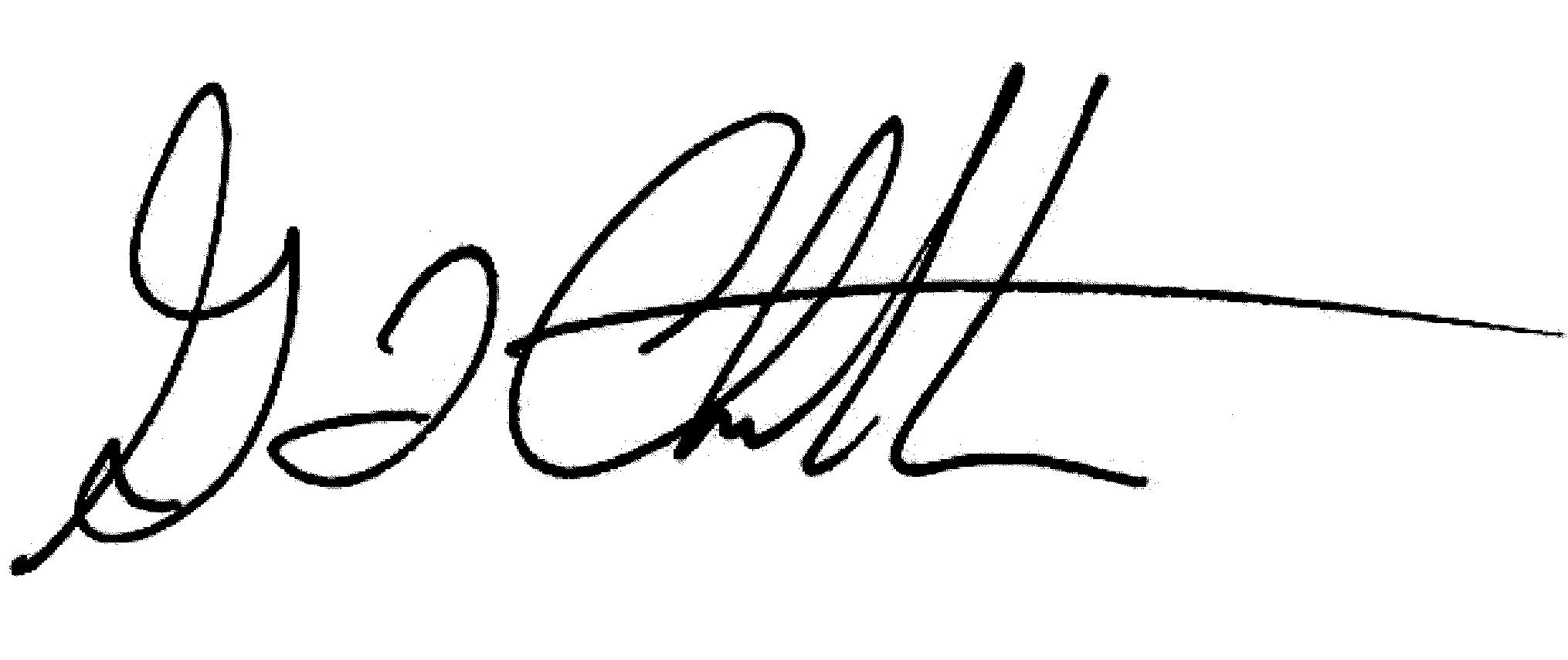
Gregory L. Christopher
Chief Executive Officer
Serious News for Serious Traders! Try StreetInsider.com Premium Free!
You May Also Be Interested In
- Mueller Industries (MLI) to Acquire Nehring Electrical Works Company for $575M
- Akanda Appoints Cooper to the Board of Directors
- ENDEAVOR ALERT: Bragar Eagel & Squire, P.C. Investigates Merger of EDR and Encourages Investors to Contact the Firm
Create E-mail Alert Related Categories
SEC FilingsSign up for StreetInsider Free!
Receive full access to all new and archived articles, unlimited portfolio tracking, e-mail alerts, custom newswires and RSS feeds - and more!